One of my favorite combinations when making bracelets is leather and charms! When deciding what color of leather to use, I chose turquoise because it’s a color that always calms me – plus it seems to work for all seasons. It reminds me of the beach where I would love to be! I decided to make this a multi strand bracelet because the stacked bracelet look is such a huge trend right now. To make your own version of this multi strand leather charm bracelet, read on. It’s easier than you think! Continue Reading…
Make Your Own Rustic Copper Heart Bracelet
December 2, 2015The popularity of bracelets just keeps increasing, and having fallen in love with some similar styles, I decided to tackle copper soldering and hand formed wire bracelet making in the same project.
Continue Reading…
Make a Tassel Necklace with Prayer Beads
November 10, 2015People use Mala necklaces for both spirituality and fashion, and making a Mala tassel necklace with prayer beads can be easy and fun! The use of Malas or “meditation garlands” in prayer dates back 3,000 years. Traditional Malas consist of 108 prayer beads, including “marker” beads, plus a larger “summit” or “guru” bead. During meditation, a mantra or prayer is recited 108 times — once per bead. The marker beads serve as a point to re-focus, if necessary, and the summit bead is a beginning and ending point. When you make your own DIY Mala necklace, you can incorporate gemstone beads with properties that benefit you (or your family, friends, and customers). You can also use charms with symbols of your choice and colors with special meanings. Read on for full instructions.
Continue Reading…DIY Team Spirit Earrings
August 31, 2015With football season fast approaching, it’s time to break out your team spirit! Colorful jewelry that shows off team colors will make it easy for everyone to know who you’re cheering for! Simply swap out the Swarovski crystal colors to make earrings that support your favorite team!
Continue Reading…
Stamp your own Longitude & Latitude Bracelets
May 5, 2015For years, longitude and latitude coordinates have been growing in popularity when it comes to fashion. They have been popping up in tattoos, jewelry and clothing. I decided I wanted to make my own longitude latitude project, with coordinates from one of my favorite places on earth, Tulum, Mexico! You can easily do this project with any location on Earth! Simply enter your desired location plus “longitude and latitude” into any search engine, and the coordinates will come up for you! —
CzechMates Memory Wire Bracelet Tutorial
September 25, 2014I love the Picasso finishes and and unusual colors of CzechMate 2-hole tile beads and other CzechMate 2-hole beads. But it’s hard to find a project with them that doesn’t involve needles and intricate beadweaving.
So … here it is! When I discovered pliers designed for looping ends of memory wire, I decided on an ombre chevron cuff bracelet. This 4- to 6-row ombre chevron design takes advantage of the CzechMate color combinations, and is easy to “string” on memory wire. The outside row uses a few seed beads (or bugle beads) near the edges, because their sizes are so compatible with these 2-hole beads.
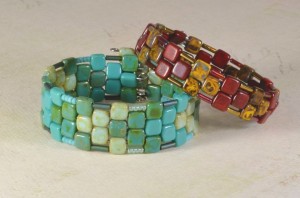
My first 2 ombre CzechMate bracelets. Rather than wrapping the memory wire around your wrist three times like most memory wire bracelets, these are cuff bracelets.
For a petite wrist, use standard stainless steel memory wire. For larger wrists or a looser fit, use stainless steel anklet memory wire. (Don’t be swayed by the word “anklet” — it’s actually an excellent bracelet size.)
Cutting Memory Wire:
When cutting any type of wire, wear eye protection, or at least make sure your bits of wire will end up someplace safe, not in anyone’s eye. Cup your free hand over the end, and aim the wire downward at a soft surface like a flocked bead mat.
Tools and Memory Wire:
Memory wire is strong, springy steel — much tougher than most jewelry wire. It requires strong, durable tools, both for cutting and bending. I tried cutting steel wire with my cheap cutters and one blade SNAPPED, shooting across the room in 3 pieces. I also dented high quality cutters that were not designed to cut steel. I strongly suggest a pair of heavy-duty flush cutters and a pair of memory wire looping pliers. They aren’t too expensive, and they work great for lighter-duty projects as well.
Step 1. Practice Making Loops:
Although Memory Wire Pliers make it easy to make consistent-sized loops, steel wire is tougher to bend than other jewelry wire. I recommend practicing memory wire loops before you begin adding beads. This helps you make all your loops at the same angle, and avoid chipping your end beads.

Cut four 2″ pieces (each about 1/4 of a circle). Practice making a loop at each end, with both loops on the same plane (or angle).
1. Grip one end of the wire firmly in the pliers and use your fingers to smoothly wrap the wire around the small side of the pliers. Don’t let it twist upward or downward.
2. About halfway around the pliers, release the plier grip on the wire, and get a new grip so you can finish making your circle.
3. Close the loop ALL the way — don’t leave a spot for beads to slide down inside a gap in the loop.
Repeat at other end. Grip the wire’s tip, push around, release, re-grip, and finish pushing. Take a look at your circles — are they the same size and angle, or are they twisting ickily in random directions? Make a few more until it’s easy to make nice consistent loops on the same plane. Also note that these loops are all to the OUTside of the circle, not the inside:
Step 2. Assemble your beads:
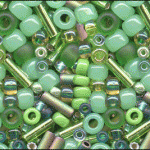
Appletini TOHO Seed & Bugle Bead Mix
TOHO seed bead mixes work excellently with CzechMate 2-hole tile beads. There are great color mixes to choose from, and you can use 3 large seed beads, 4 small seed beads, or a single bugle bead as perfect-size spacers.
A few beads from each assortment are too tiny to fit on memory wire, or too big to fit next to a Czechmate, so save those for future projects.
Step 3. Make the bracelet:
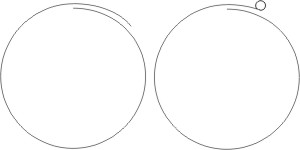
3a. Cut 4 pieces of wire, each 1 to 1-1/8 coil long. Make sure they are all the same length.
Carefully round 1 end of each wire.
For a 1-color bracelet, use approximately 42 beads. For a 3-color bracelet, count out 15 tile beads of each color in sets of 3. Lay them out in the order that you’ll use them. You might not use all the beads you laid out, but it’s easier to keep your pattern going correctly if you lay out the beads in advance.
3g. After your last 2 beads, push beads snug (but not super tight), and trim wire to approx. 1/2″ if necessary. Next, very carefully round the end wires for both strands (one wire at a time). Abrupt / harsh movements may chip the end bead.
Take another of your prepared wires, and string 4 seed beads, or a single bugle bead. Place these next to your strung CzechMates … do they look good? If not, pick a different color or size and test it before you begin the next step.

3h. Back at the beginning, feed a new piece of prepared wire through the other hole in one of your first beads.
3i. Where the wire comes out, add 3-5 seed beads (or a bugle bead) so they are the same total length as a Czechmate tile bead or slightly shorter.

3k. Repeat for 4th row, trim excess if necessary, and carefully round the ends. (Click image for close-up.)
Tips & Errata:
Do your best to make the loops all face the same direction, but don’t be hard on yourself if they don’t. Here is my first bracelet, with wonky ends and a chipped bead. When I taught a class on how to make this bracelet, I introduced the “practice making loops” step, and not a single person chipped a bead!
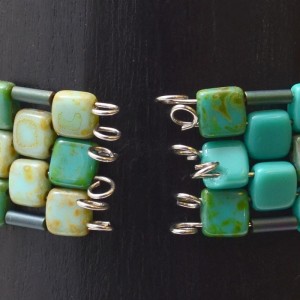
Close-up of bad loops on my first bracelet. The tips listed above should help you make better loops and avoid chipped beads.
By my 3rd bracelet, I realized it’s much easier to finish the ends if the strands (after looping) are tiny bit shorter than one full coil, so now I design these more like cuffs than bangles.
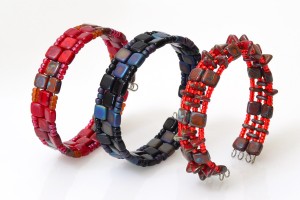
It’s much easier to finish the ends, if each strand, after looping, is slightly shorter than one full coil, more like a cuff than the bangles I originally envisioned.
You’ll soon perfect your ability to make all your loops at the same angle. After that, these are quick and easy to make, so make a bunch for gifts or to sell!
Depending on the size of your spacer beads, some bracelets spike up a bit in the middle, and others curve up at the outside edges. This is part of the fun with these designs. Used in this pattern, I think the CzechMates™ Two Hole Triangle Beads look like tiny Stegosaurus / dragon spikes.
Parts & Supplies:
- Stainless Steel Memory Wire for a petite wrist (or Anklet Wire for an average to large wrist)
- CzechMates 2-Hole Beads (I used Tile Beads for all of my bracelets, and added Triangle Beads to one.)
- TOHO Seed Bead Mixes
- Memory Wire Looping Pliers
- Heavy-Duty Flush Cutters
- Safety Glasses
- Flocked Bead Mat (optional)
Any questions? Please ask! (Click on “Comments” or “Leave a Reply” below.)
Say it Your Way with Easy Metal Stamped Jewelry
September 10, 2014You don’t have to be Frank Sinatra to do things your own way! That’s the beauty of metal stamping as a jewelry technique. Not only do you get to assemble components, you get to make your own components – and they can say whatever you want them to say!
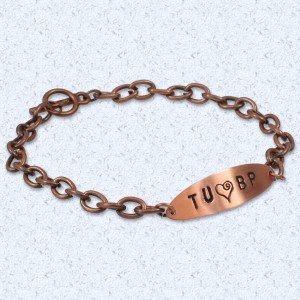
This Young Love bracelet is a perfect example of how you can easily customize jewelry with metal stamps!
Letter stamps are the perfect way to create monogram jewelry, plus jewelry with names or inspirational sayings. Design metal stamps are the perfect way to add cuteness and panache.
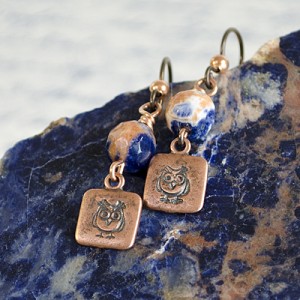
Learn to make these simple metal stamped earrings – just click the image above for the complete parts, ready to buy.
Designer Amy Mickelson’s “Hootie and the Sodalite Earrings” feature custom owl charms she made using an ImpressArt Metal Stamp and a JBB Antiqued Copper Plated Square Tag Charm. These JBB tags are plated especially for stampers – pretty amazing! For more on these components, see the full parts list and tutorial here.
The basics of jewelry stamping are easy and only require a few tools. The tools are a small investment, but will last for years and thousands of impressions!
Supplies you’ll want:
- Letter stamps and/or design stamps
- A steel bench block (the block pictured is #69-123 combo block)
- A Brass hammer (the hammer pictured is #69-346)
- Metal blanks & tags – choose from 100’s of options!
- Optional: Stamp Straight Tape
The basic steps to jewelry stamping:
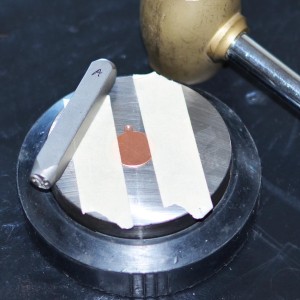
Once you’ve planned your design, secure your metal tag or blank onto your steel block with tape. Stamp Straight Tape by ImpressArt is more expensive than masking tape, but it offers a sturdier edge and does not leave sticky residue.
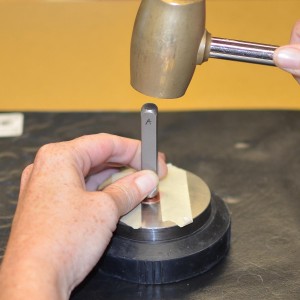
Strike the perfectly vertical stamp with one firm blow. This is important for achieving a clear impression.
That’s all there is to it! It really is that simple. Then, you can use your completed stamped charms to make earrings, necklaces, bracelets, gift tags, and more!
For a great monogram jewelry tutorial, see “Ava’s Ladies in Waiting” Necklace Tutorial in our Design Gallery.
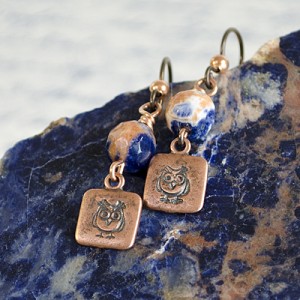
Click this picture for all the parts and instructions you need to make adorable metal stamped owl earrings.
To make fun owl earrings, see the “Hootie and the Sodalite” Earrings Tutorial.
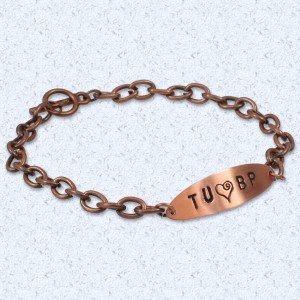
Click this picture for all the parts and instructions you need to make a simple metal stamped bracelet.
For the full how-to on making a metal stamped chain bracelet, see our “Young Love” Bracelet Tutorial.
Rings & Things offers a huge variety of metal stamping blanks, plus jewelry stamping tools and supplies with fast shipping and free returns.
So what are you waiting for? Isn’t it time to say things your way! ~ Melissa
How to make Wire Links with Wubbers Mandrel Pliers
August 7, 2014
If you are looking to expand your tool selection, Wubbers® Pliers are a great addition to any jeweler’s bench. The pliers have comfy padded handles, are made of high quality stainless steel, and have box-joint construction. Wubbers offers traditional jewelry pliers in two sizes (which are awesome), but the pliers that caught my eye are the mandrel pliers. Mandrel pliers are available in several shapes and sizes. And best of all, they are perfect for forming wire links, like those featured in designer Polly Nobbs-LaRue’s two blog posts on making soldered-link bracelets: “I Love Copper Solder!” and “Copper Soldering Tutorial – Part 2”.
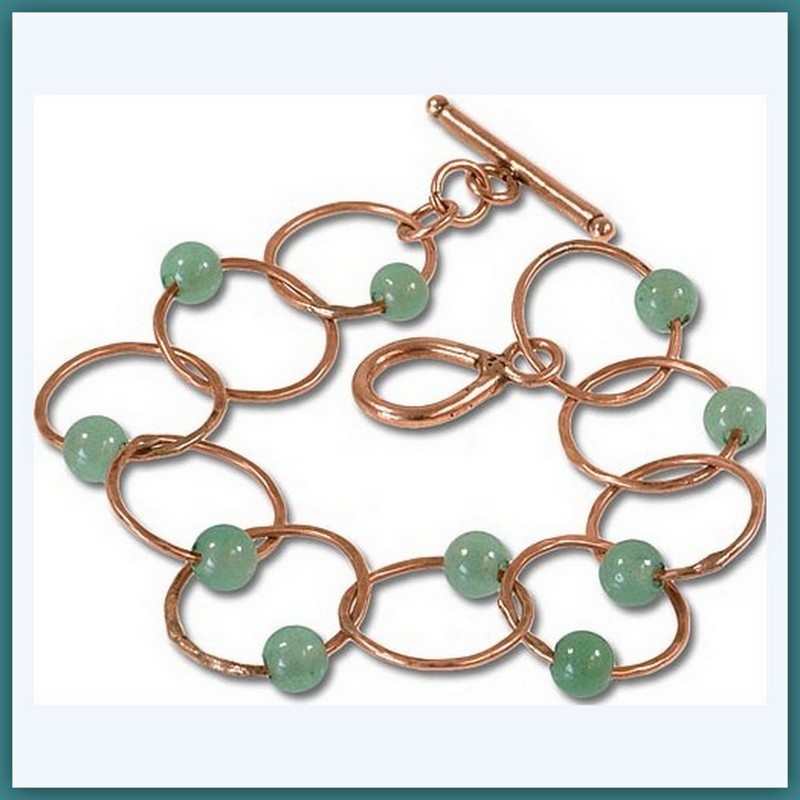
“Captured Aventurine” Bracelet Tutorial by Rings & Things’ designer Polly Nobbs-LaRue
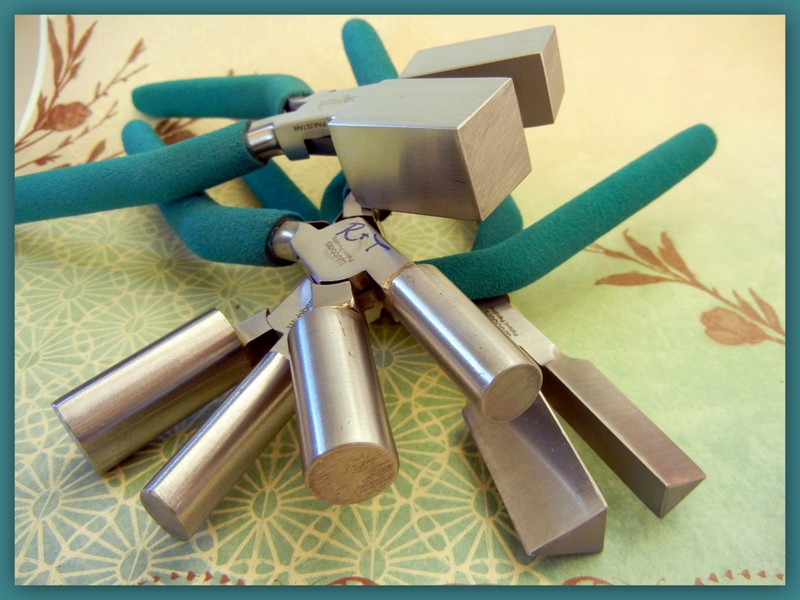
Wubbers mandrel pliers are available in several shapes: round, square, triangle, oval, and half-round (not pictured). Each shape is available in a variety of sizes. Plus each pliers’ jaw has two mandrel sizes.

Check out the Wubbers packaging for gauge recommendations and an access code for Wubbers University.
An added bonus: inside each package is your invitation and access code for free online classes and tutorials at Wubbers University! You will find a wide variety of classes for the beginning to advanced jewelry maker; just what you need to build new skills.
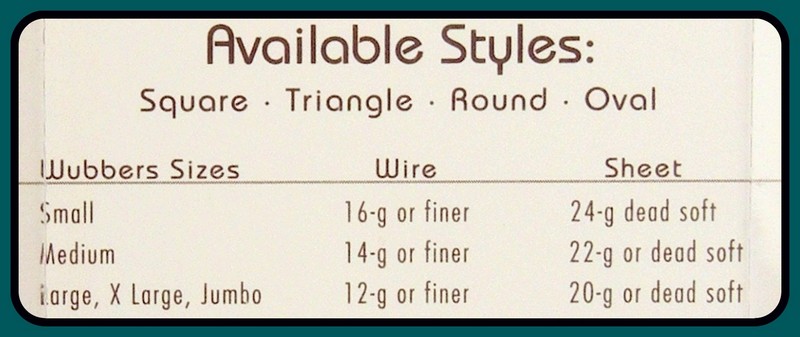
Follow the wire and sheet metal gauge recommendations for your size of mandrel pliers — an easy to follow chart is featured on each package.
Recommended tools for the jeweler’s bench:
- Nylon-jaw flat-nose pliers for straightening the wire
- Wubbers mandrel pliers for forming the wire
- Jewelers saw frame and saw blades for cutting the wire
- Swivel vise for holding the wire coil (and so many other valuable tasks!)
- Bench pin for holding the wire coil
- Flat-nose and chain-nose pliers for aligning the cut wire ends
Follow these steps to form and cut wire links using Wubbers mandrel pliers and a jeweler’s saw:
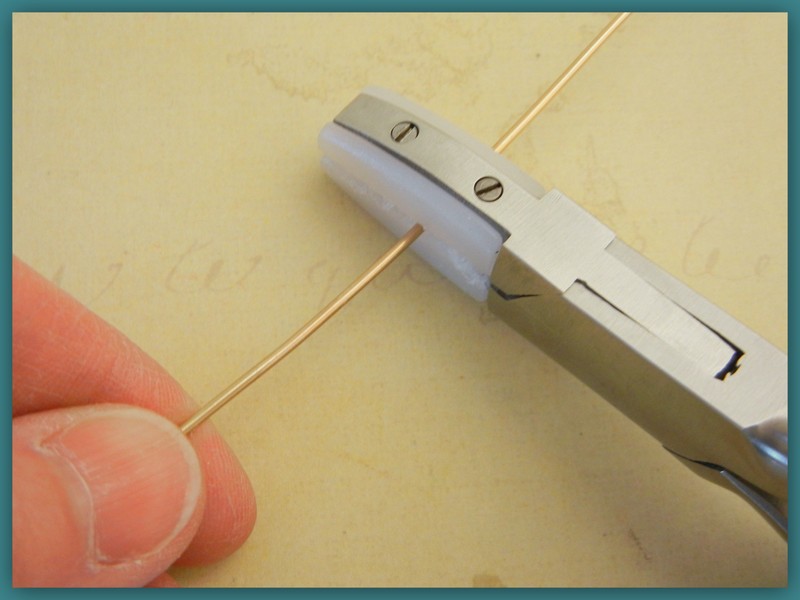
Step 1: Begin by straightening the wire. Pull the wire through nylon-jaw flat-nose pliers to easily straighten it. If you are planning to solder your links, avoid plated wire; instead use solid brass, copper, nickel, sterling or silver-filled wire.

Step 2: Begin wrapping the wire around your mandrel of choice. As you coil, maintain even pressure so the links come out uniform. With the round mandrels, you can rotate the wire on the mandrel to make a continuous coil; for other shaped pliers, you will need to open and close the pliers’ jaw with each complete pass.

Step 3: Continue coiling the wire. Make a coil that is two wraps more than the number of links you need; the first and last coil will not make a complete link.
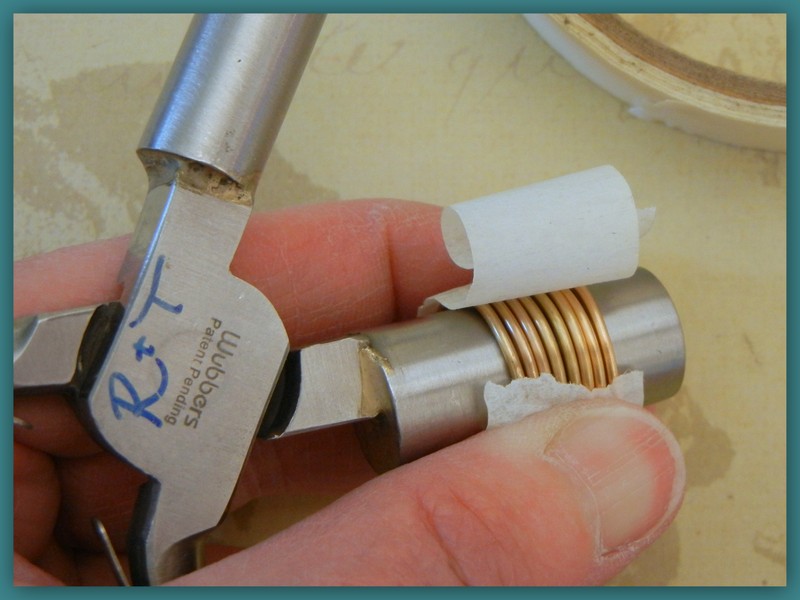
Step 4: Pinch the wire coils tightly together, and apply a layer of low-tack masking tape around the coil. This will keep the wire in place while sawing. Slide the taped coil off the mandrel pliers.
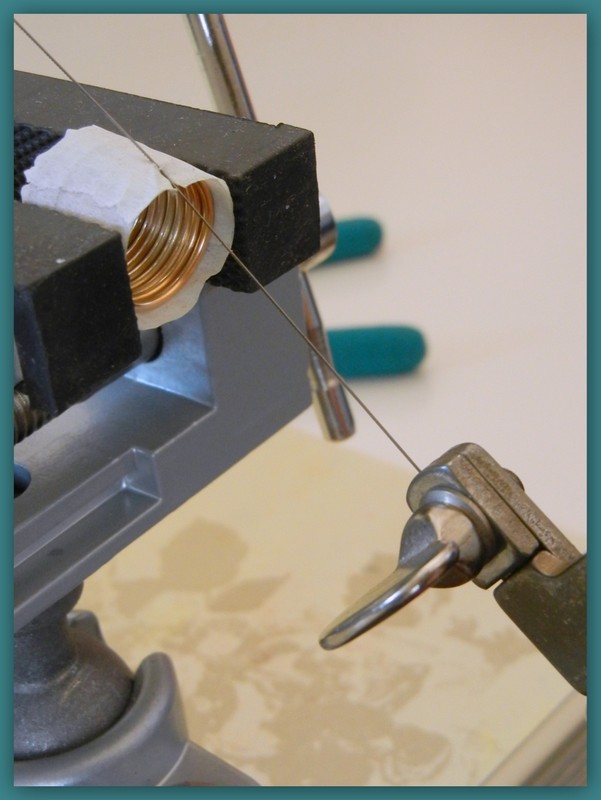
Step 5 – Version A: Attach a swivel vise to your workbench and place the wire coil in the padded jaw. Gently tighten the jaw so the wire coil is held firmly in place–but not so tightly the coil becomes misshapen. Thread your jeweler’s saw with the blade’s teeth facing down and out. You are ready to begin sawing. To avoid nicking the wire, angle the saw blade slightly so the blade only touches the wire being cut.

Step 5 – Version B: Attach a bench pin to your workbench and firmly hold the wire coil on the edge of he pin. Use a jeweler’s saw to cut the wire coil from top to bottom. To avoid nicking the wire, angle the saw blade slightly so the blade only touches the wire being cut.

Step 6: Use flat-nose and chain-nose pliers to align the cut ends of the wire links. The cut ends need to fit snugly together for soldering. Your wire links are ready to solder.
Make things!
Mollie
Beadalon® Wire Banding Pliers
August 20, 2013The initial bends when trying to band wire together can be frustrating. I have tried every tool, hoping to find something that would accurately bend wire into two perfectly-placed right angle bends without marring it. Now there is a specialty tool made just for perfect double right angle bends — Beadalon Wire Banding Pliers!
I am a perfectionist in the jewelry I create, and the last thing I want to do is fight with the very beginning of the project and end up with scratched banding, or having the banding bend be just a little off. Not only is it frustrating, but the accuracy of the banding can make or break the entire piece.
This tool is very easy to use — now you can quickly create two right angle bends close together, so you can neatly band the remainder of your wires together. We have created the graphic tutorial below to help you to learn how to use these cool wire banding pliers.
Please visit our Design Gallery for 100’s of free jewelry projects / tutorials, but we apologize that as of 2015 during a site upgrade, the 2 wire wrapping projects projects below have retired.
Although Rings & Things no longer sells any banding pliers, we’ve kept this infographic for those of you who already own some and need a quick refresher:
Concrete in Jewelry
July 29, 2013An industrial material such as concrete seems unlikely for jewelry, but it works very well! It is relatively lightweight, and very durable. It is great for personalized adornment, because you can embed virtually any charm, bead or found object you want.
Visit our design gallery for free jewelry projects and check our Mosaic Jewelry Board on Pinterest for concrete jewelry inspirations.
Difference Between Cement and Concrete
Cement is a powdered ingredient (mostly calcium silicates) used in concrete. It is strong, but brittle and susceptible to scratching. When mixed with water, it undergoes a series of chemical reactions and slowly crystallizes into a strong, interlocking form. Concrete is a mixture of cement, an aggregate (sand or gravel) and water.
Jewelry Grade Concrete
EuroTool created EnCapture Artisan Concrete specifically for jewelry artists. This new kit makes it easy for designers to create small mosaics and concrete jewelry. For information on making your own concrete, visit Ganoksin.
Creating with Artisan Concrete
Tips on Using EnCapture Artisan Concrete
Coloring Concrete
Prismacolor colored pencils can be used to color the surface of concrete! To prepare the surface, wet-sand it using fine-grit, wet/dry sandpaper and let dry for 24 hours. To seal the color, spray with several light coats of Krylon UV sealant.
Safety When Using Concrete in Jewelry
Always use disposable cups and utensils. Throw away unused concrete; do not wash it down the drain (it will clog pipes). Wear a respirator, safety glasses and gloves.
Have Fun & Happy Creating!